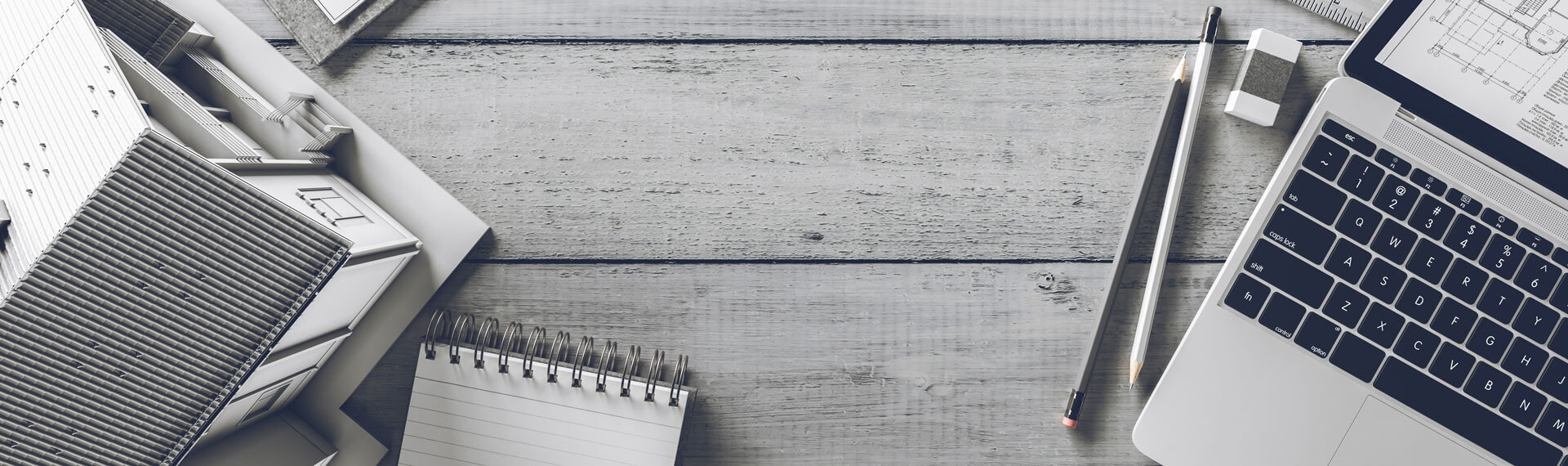
Frequently Asked Questions
The extruded profiles size is limited by the size of our bigger, 3750tonns, press. A general rule is maximum width of 330mm and maximum height of 180mm but not combined together. Depending on the requested shape factor you can get a more precise answer from our technical team.
Solid refer to a shape with no cavities at all, like flat bars or rods. Semi-hollow is a shape that is partially enclosed but always keep a gap open, even very small. Hollow shapes contain one or more totally closed areas like a tube.
ALUMIL follows the internationally accepted system of EN Regulations for aluminium extrusion and products. Specifically we can accept EN-755 or EN-12020. In its chapters all tolerances of geometry and shape is clearly defined. On request we can agree on special tolerances for critical dimensions.
Any change on a manufactured die is a matter of a new agreement between the company and the customer. After contacting the technical department our die experts will evaluate the capability of any change and can propose the best solution, depending on time needed and cost.
In this way, we have a formal agreement between the customer and the company before a die is ordered for manufacture. By signature and stamp a customer accepts, the geometry, dimensions, tolerances, primary surface and finish if indicated. This procedure is also an additional way for both sides to confirm the agreement on all technical aspects.
The extrudable wall thickness depends on the geometry of the profile and specified material. Each time of a new request our die specialists discuss with the customer about wall thickness presented on his drawing and propose if needed any wall thickness change for facilitating the extrusion process without affecting the usability of the profile.
Proper packaging based on the real needs of each customer is a critical part of the production process and can increase or save the cost of the final product. By defining the way of packaging, we can proceed with accurate cost calculation and therefore to offer precise final prices. However, there are default packaging options that you can choose accordingly.
The final length of the purchased items is vital for the routing of production since bigger lengths can be cut directly on the press while shorter may need special cutting in a separate division. That could consume more time and add more cost that should be calculated before we quote.
The choice of the right alloy is critical for all stages of production and quality of the final product. Apart from the cost of the products, specific alloy characteristics affect the design and manufacture of the die and the mechanical properties of the final extrusion. As well it affects the capability of machining or surface treatments.
Sampling is a necessary part of an initial production. After successful ordering of the die, we run a trial extrusion and keep samples on request of our customer. These will be forwarded for validation, after which we can continue with serial production. This process is followed on every new die made upon request.
Alumil S.A. is producing a wide range of architectural building systems, but as well it can serve any client need on custom design profiles. Different aluminium alloys, machining, and surface treatments can lead to the product you have imagined.
Alumil S.A. is cooperating with a wide range of companies around the world, who are involved on numerous sections of industrial production. From smaller or larger industries that incorporate aluminium in their products or use for manufacturing their machines and facilities to any individual that needs an extrusion.
Alumil's extrusion & machining unit develops strong B2B relations with its final customers. However, any individual or educational institutes can approach us for orientating on how they could proceed with applying their idea in force. Our team will investigate and provide technical and financial details and if parts agree we can move to serial production and selling.
Alumil is certified as per ISO 9001, ISO 14001, OHSAS, GSB for coating, QUALICOAT and QUALANOD from highly recognized partners.
Alumil S.A. is certified for the CE mark for all products that is selling.
Design of a new profile is based on the functionality that its use demands and the possible collaboration with other profiles or accessories. It is a job that should take into consideration the mechanical stresses, the dimensional accuracy and the aesthetics of the final product if it is visible to the user. In any case, it should be carried out by experts who are the ones that can incorporate all the above in a single drawing.
Apart from the product itself, our most important provided service is the holistic product and customer support. Giving advise from the phase of design to the optimization of production, packaging, and delivery based on your specific needs. We offer you the opportunity to model and visualize your product before real output with the use of a 3D printer. And of course, we provide a call center with technical and financial representatives always at your disposal.
Surface treatments are among our specialties. We can powder coat any profile using the entire palette of RAL colors on all available textures (glossy, matt, sable) or even develop custom colors upon sampling. We can also imitate wood with the use of dedicated color films. And of course, our top quality surface treatment, anodization accompanied with special finishes like shot blasting, brushing or polishing that upgrade not only the aesthetics of your profile but also enhances the durability of the profile against harsh conditions. The latest addition to our range of surface treatments is pre-anodization that provides the ultimate protection of anodization against corrosion along with the wide choice of any RAL color.
Die construction is a very delicate process handled over to our highly experienced suppliers. Depending on the size and the complexity of the geometry, a die can be finalized from 3-5 weeks time.
Calculating the mass of the material that you will need can be simple if you know the total length of a profile that will be ordered. The first job is to calculate the area of the cross-section of the desired profile by hand or by using appropriate CAD software. Next, we multiply the area that we calculated before by the total length we are going to use to get the total volume of material. At last, we multiply the volume by the density of aluminium which is always constant and equal to 2,71gr/cm^3, and we get the total mass of the quantity.
Our extrusion division can produce with most of 6xxx series alloys. Usually, we extrude using 6060, 6063, 6005 and 6082, alloys that satisfy the majority of product properties and customer needs but on request, we would be able to agree on another alloy within the series.
Packaging is a process of high importance for us since it can adequately protect and maintain the quality of our products. Options are limitless with different outer materials (wood, paper, plastic) and inner interleaf (paper, plastic, protective self-adhesive foils). Please contact our team for detailed presentation and personalized proposals.
The actual lead time varies from 3 to 6 weeks depending on the desired surface treatment (MF profiles, painted or anodized profiles), the desired additional manufacturing process (special cutting in a specific length, machining, CNC treatment, etc.) always taking into consideration the actual production capacity.
To finalize the drawing, before your confirmation on it, we would undoubtedly need files in Autocad format (.dwg or .dxf). However, for a first inspection, we could use detailed .pdf files.
If a surface of your desired profile is going to be visible and needs highest quality handling, please be sure to indicate this on your drawing. Having this information available, we will be able to treat and finish it with the best possible quality standards.
For any not specified corner radius, we follow the rule of a minimum 0,2mm radius.
The manufacturing cost of a die highly depends on the desired geometry and its complexity, the desired alloy and the nature of the die (flat, hollow, etc.). After receiving this information from the customer, we get a different quote each time from our die supplier.
The minimum order quantity varies from 500kg to 2000kg, depending on the size and the weight of the profile.
Lead time for a trial sample extrusion will be given to each customer after providing the desired quantity and length of the samples.
Actual die life varies from 60 to 100metric tons, depending on the type of the profile (solid/hollow/semi-hollow), the alloy selection, the desired extrusion surface, and dimensional tolerancing.
This cannot be done since the die was manufactured for a different press and will not be able to fit on ours.
Alumil provides a wide range of possible machining on your profiles. In-house we operate a separate division with CNC machinery that can handle almost any job requested. Also, there is a dedicated division that manufactures small or bigger accessories that require cutting, drilling, assembly, sandblasting, etc.
Our experienced team will be at your disposal anytime to advise on the phase of product design.
Our activity is limited to aluminium extrusion but if you request a reliable partner for a different material we can propose a related company. Especially for plastic pieces or gaskets, we have some of the best solutions.
Yes
No entries found with the specific search criteria.