ALUMIL BEYOND
Sustainability – Sustainable Development – Social Contribution
In ALUMIL we look beyond. Beyond the boundaries of our industry. Beyond our business activities. Our planet needs our contribution. This is why we envision a world of sustainable development and social contribution. A world beyond the ordinary or otherwise… the world of ALUMIL BEYOND.
Our Achievements in numbers
Sustainability Report 2023
Read the annual ALUMIL Sustainability Report, which
records the performance and the achievements of the company on social
responsibility, environment, corporate governance, market, and human
resources issues.
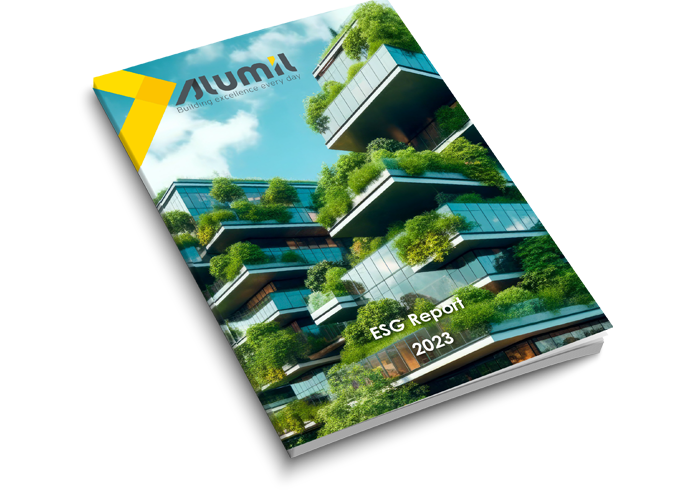

«We are developing our ESG strategy, having in mind that companies can and should actively participate in the major challenges that humanity is facing».
- Georgios Mylonas, President and CEO of ALUMIL
We incorporate the Sustainable Development Goals of the United Nations
Awards & Recognition
Read about our corporate actions
Contact
For sustainable development and corporate social responsibility issues, please fill out the form with your details and we will contact you.
Contact form